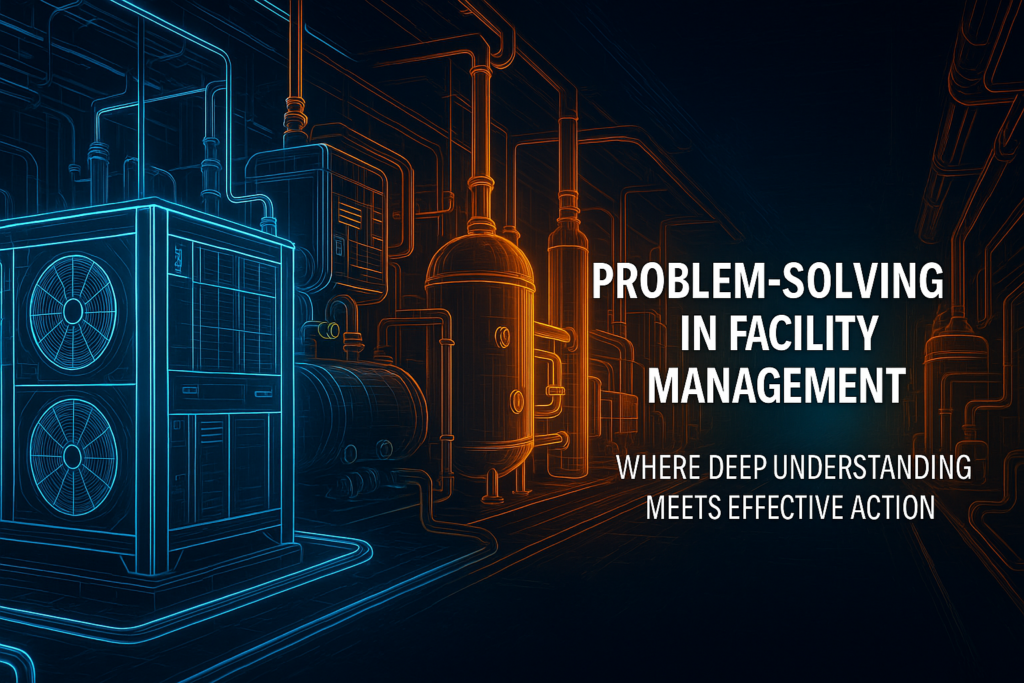
In today’s rapidly evolving facility landscape, problem‑solving is more than a reactionary task—it’s a strategic practice. Whether we are addressing a malfunctioning air‑handling unit (AHU) during a seasonal transition or calibrating a static pressure sensor on a critical exhaust fan, our success hinges on the depth of our understanding.
Drawing on sociological, philosophical, and political dimensions of solidarity—as explored in Durkheim’s concepts of mechanical and organic bonds, Habermas’s communicative reason, and Shultz’s typology of social, civic, and political unity, we can reframe technical troubleshooting as a shared endeavor that integrates human expertise with advanced technology.
This article blends theoretical perspectives with real‑world scenarios from facility management, illustrating how a holistic grasp of systems, people, and data drives more effective solutions.
1. Reframing Problem‑Solving Through Solidarity
“Solidarity is a sense of unity, cooperation, and shared fate… an antidote to fragmentation.” —Solidarity: Bridging Societal Divisions
- Mechanical Solidarity in FM Teams
In tight‑knit maintenance crews, trust is built on shared routines—morning work orders, familiar tools, and tacit know‑how. This “mechanical” bond creates the psychological safety needed to speak up when equipment readings look off. - Organic Solidarity Across Disciplines
Modern campuses rely on diverse experts—controls technicians, data analysts, AI modelers. Our interdependence mirrors organic solidarity: we depend on each other’s specialized skills, even if we rarely work side‑by‑side. - Communicative Reason on the Plant Floor
When we gather around a trending chart in the BAS, we enact Habermas’s principle: rational dialogue. Each voice—mechanic, engineer, or vendor—offers data points and intuitions that converge on a shared diagnosis.
Takeaway: By recognizing solidarity as the social glue of troubleshooting, we cultivate collaborative intelligence that outperforms any single perspective.
2. Theoretical Foundations Applied to Facilities
Theoretical Lens | Core Idea | Facility‑Management Translation |
Durkheim – Mechanical vs. Organic | Unity from sameness vs. interdependence from specialization | Small maintenance crews vs. multi‑disciplinary energy teams |
Habermas – Communicative Reason | Rational discourse builds understanding and legitimacy | Daily huddles review fault analytics before dispatching work |
Shultz – Social, Civic, Political Solidarity | Identity‑based, state‑mediated, and justice‑oriented unity | Toolbox talks, safety policies, and sustainability task forces |
Enlightened Self‑Interest | Helping others ultimately benefits oneself | Sharing control‑sequence tweaks across buildings reduces callbacks |
These frameworks remind us that technical competence thrives in a culture of mutual support, transparent dialogue, and shared purpose.
3. Translating Theory to Practice: Three Scenarios
Scenario 1: Optimizing AHU Staging During Seasonal Change‑Over
Context: Our university’s OA supply unit (BLDG1‑AHU01) struggled with humidity spikes each April. The PPCL script supported staging but lacked adaptive thresholds.
Problem‑Solving Steps
- Communicative Mapping: Controls, HVAC, and energy specialists gathered trending data and occupant feedback.
- Shared Analytics: An AI model predicted coil load vs. outside enthalpy, highlighting that reheat staging lagged by 15 minutes.
- Collaborative Rewrite: We rewrote Section 9: System Occupancy Control in PPCL to include an enthalpy‑driven pre‑cool bias.
- Outcome: Supply‑air dewpoint stabilized within ±2 °F, and chilled‑water ΔT improved 18 %, saving $12 k annually.
Solidarity Lens: Organic solidarity—controls coders and field techs relying on each other’s expertise—delivered a systemic fix.
Scenario 2: Static Pressure Sensor Calibration in an Exhaust Fan
Context: Filter alarms traced back to a sensor reading 0.25 “WC low. Two sensors covered the plenum.
Problem‑Solving Steps
- Mechanical Solidarity: A two‑person crew trusted each other’s field checks.
- Tool‑Enhanced Insight: Using a Bluetooth manometer and CMMS‑linked calibration app, we mapped drift over time.
- Root‑Cause Dialogue: Discussion with purchasing uncovered that a recent batch lacked factory zero‑adjustment.
- Outcome: Replacement and calibration cut nuisance alarms by 90 %, freeing 40 labor‑hours per quarter.
Solidarity Lens: Mechanical solidarity enabled swift teamwork, while technology supplied high‑resolution data.
Scenario 3: Troubleshooting a Bray Series 70 Valve Actuator Fault
Context: After a campus training, one AHU reported erratic VFD feedback. Diagnostics pointed to a stalled actuator.
Problem‑Solving Steps
- Civic Solidarity: Vendor representatives joined our call, sharing firmware logs.
- Digital Twin Test: We replayed the fault curve in a sandbox BAS emulator to replicate conditions safely.
- Iterative Calibration: Using the Series 70 auto‑cal routine, we reset limit switches and verified 4–20 mA feedback range.
- Outcome: Valve modulation restored; estimated chilled‑water bypass reduced by 8 %, equivalent to $3 k energy savings.
Solidarity Lens: Civic solidarity—state‑mediated safety policies and vendor warranties—framed cooperative problem resolution.
4. Technology Meets Expertise: A Synergistic Model
- IoT & Edge Analytics – Real‑time data acquisition exposes hidden patterns (e.g., fan‑coil valve hunting).
- AI‑Driven Diagnostics – Predictive models flag anomalies before comfort degrades.
- CMMS & Digital Records – Linking work notes, photos, and sensor snapshots ensures institutional memory.
- Cloud Collaboration – Shared dashboards allow cross‑campus specialists to co‑triage faults asynchronously.
Human Role: Interpretation and ethical judgment. Algorithms suggest; technicians validate, contextualize, and act.
Deep understanding is the bridge between raw data and meaningful action.
5. The Solidarity Loop for Continuous Improvement
- Detect – Technology senses deviation.
- Discuss – Teams engage in communicative reasoning, blending diverse viewpoints.
- Decide – A shared hypothesis forms; responsibilities are assigned.
- Do – Field execution leverages best‑fit tools and skills.
- Document – Outcomes feed back into CMMS, training modules, and AI datasets.
- Develop – Lessons inform design standards, policies, and future automations.
Repeated iterations convert isolated fixes into systemic resilience.
6. Implementation Guidelines for Facility Leaders
- Foster Psychological Safety – Encourage questions and admit uncertainty; expertise grows through collective inquiry.
- Codify Knowledge – Embed control logic explanations and calibration photos directly within BAS graphics.
- Leverage External Partnerships – Engage vendors and academia in fault labs; civic solidarity expands problem‑solving capacity.
- Invest in Data Literacy – Train technicians to interpret trend plots and AI alerts; human insight amplifies digital tools.
- Align KPIs With Shared Values – Energy savings, occupant comfort, and labor efficiency are mutual wins.
Conclusion
Problem‑solving in facility management is neither purely technical nor solely human. It thrives at the intersection where deep theoretical understanding, collaborative solidarity, and data‑driven technology meet.
When we draw on diverse knowledge—mechanical experience, AI analytics, sociological insight—we move beyond quick fixes toward root‑cause, value‑aligned solutions. By nurturing solidarity in our teams and integrating advanced tools, we not only repair today’s faults but build adaptive systems ready for tomorrow’s challenges.
Key Message: The depth of our understanding determines the height of our solutions.
Action Steps for Our Team
- Schedule a monthly Solidarity Huddle to review cross‑disciplinary case studies.
- Expand the Knowledge Hub with annotated fault curves and PPCL snippets.
- Launch a pilot AI‑driven predictive maintenance program on the Dormitory AHUs within Q3.
Together, we transform challenges into learning loops and elevate facility performance—one insight, one fix, and one act of solidarity at a time.